In the world of electronics manufacturing, two central themes are currently in focus: Smart manufacturing lines and sustainability. These topics are of great importance, both from an ecological perspective and in terms of operational efficiency. The leading trade fair for electronics manufacturing has accordingly aligned itself with these priorities and emphasizes the areas of Artificial Intelligence (AI) in electronics manufacturing, power electronics as a crucial factor for a sustainable world, and the application of sensor technology in electronics manufacturing. Discover the latest developments in resource conservation, automation, and digitalization by Rehm Thermal Systems in Hall A4, Booth 335, and become a part of the transformation towards a sustainable future. True to this year’s trade fair motto: “Be pART of digitalization, automation, transformation, diversity, responsibility, and sustainability.”
VisionXP+ – The new generation of energy-efficient soldering systems
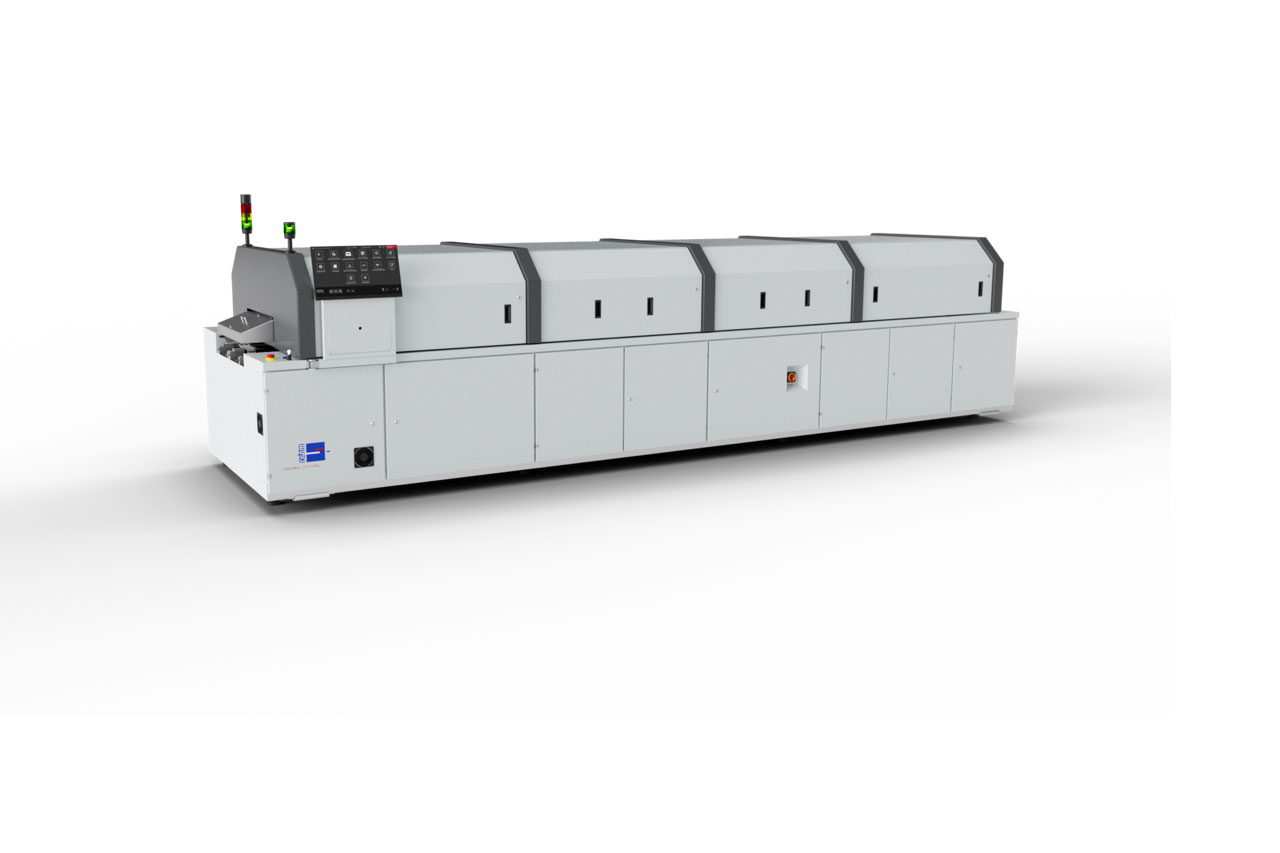
A significant energy-saving factor of the VisionXP+ series is the EC fan motors integrated for some time now, which not only make the system noticeably quieter but also more sustainable and allow for a more stable and simplified temperature profiling. Each zone can be both heated and cooled, enabling an ever-optimized energy state and ideal zone separation.
Additionally, Rehm has developed ProMetrics, a tool that ensures process stability and efficient profiling, with a focus on reducing resource consumption. Another highlight is the new 3-stage Eco-Mode, which allows you to save energy and nitrogen based on the system’s idle state. However, software-based solutions are not the only contributors to energy-efficient soldering processes. Optimized system technology plays a significant role: Improved residue management, new cooling section design, optimized gas handling, and, not to forget, the new mechatronic curtain at the system’s entrance and exit, which virtually eliminates nitrogen escape into the environment, are groundbreaking for sustainable electronics manufacturing. Using the mechatronic curtain alone can save up to 20% of nitrogen.
The new cooling section design, with a 30% larger residue separation area, extends the filter and agglomerator lifespan by a factor of 3. Flexible cooling gradients are achieved by individually setting each zone through direct control of the EC motors.
The core of the new system generation, the optimized and energy-efficient gas handling in the cooling section, can be experienced live at the booth with an AR showcase. Immerse yourself in the soldering process and see what happens in the system.
I
Innovative production line concepts with the ProtectoX series
Smart factory concepts and line integration are other key focuses that are shaping the industry. The demands on the new generation of manufacturing systems have constantly grown. Today, it’s no longer just about individual machines, but about line solutions, with “turnkey” being the keyword. Setting up a completely new line requires appropriate technological process understanding to coordinate and implement the necessary tests and evaluations when the complete coating process is still uncharted territory in manufacturing, this becomes even more complex.
For Rehm Thermal Systems, the concept of a turnkey solution not only focuses on equipment but, more importantly, on the complete dispensing process. This involves the consideration of whether in addition to the pure painting process, sealing, bonding, and dispensing applications should also be provided. Visit our on-site experts to see the diverse possibilities of our portfolio in the Conformal Coating and Dispensing sector. These systems come with numerous features that simplify the coating process and ensure process reliability. A height sensor with Z-positioning ensures optimal compensation when dispensing assemblies that are not planar due to their characteristics. Since the height must remain constant, automatic height adjustment is essential for a safe process. Another advantage is the 2D programming on 3D objects. Programming is done in 2D, the height sensor scans the adhesive path of the component being dispensed and automatically generates the height contour. This automatically creates the appropriate program for this component. With the ViCON Protecto system software, only a few steps are needed between the assembly layout and the final coating. Meet our on-site experts and also see the new integrated 3D height sensor of this coating and dispensing system.
Resource-efficient vapor phase soldering with the Condenso series
In the world of vacuum soldering, vapor phase soldering systems have been a proven technique for decades to significantly reduce air inclusions in solder joints. From the start, Rehm integrated a closed-loop system for the injected Galden® medium into the Condenso series of vapor phase soldering systems, making it a sustainable solution for the future.
The principle is equally efficient and resource-friendly. After soldering, the vacuum and/or cooling process starts. Simultaneously, the process gas is extracted and cleaned. The extraction creates a vacuum, which also guarantees rapid drying of the solder and the process chamber, minimizing losses when ejecting products.
The extracted Galden® is filtered and cleaned of impurities using a granulate. Approximately 99.9% of the medium can be recovered in this way. The cleaned fluid is stored at room temperature and made available for further processes. This eliminates evaporation losses and energy losses. The hermetic isolation of the process chamber (simultaneously a vacuum chamber) also eliminates “evaporation losses” during soldering. In addition to minimal maintenance, lower operating costs are achieved through reduced medium consumption.
When developing the CondensoXS smart condensation soldering system, the primary focus was on the process chamber, ensuring the highest process security while maintaining a compact footprint. It impresses with a new chamber design and flexibility throughout. The new vertically opening and closing chamber ensures optimal hermetic sealing, ensuring reliable and reproducible results. Flexible cooling options, vacuum, and injection principles also guarantee reliable processes in a semi-automated production environment with medium production volumes.
At our booth, you can see both the CondensoXS smart and the smaller batch solution, CondensoXC, equipped with the intuitive ViCON Condenso system software.
Contact soldering for power electronics with Nexus
The Nexus soldering system guarantees the best results through reflow soldering processes with contact heat under vacuum, meeting the highest requirements in the field of advanced packaging and power electronics.
The Nexus has been optimized through the selection of new materials and years of market experience. It is ideal for void-free soldering of various components (e.g., IGBT) on DCB substrates. The assembly of materials from different substances mostly takes place under vacuum at temperatures up to 400°C (optionally 450°C). The activation of the component surface is achieved through various process gases, including hydrogen combinations. An integrated bubbler system, mainly using formic acid, ensures optimal doping and is implemented close to the process in the system. The components remain in a fixed position throughout the soldering process in the Nexus, ensuring they are not in motion. Furthermore, the Nexus boasts the largest working area on the market, meeting the most economic and flexible requirements.
About Rehm Thermal Systems
Rehm Thermal Systems is a specialist in the field of thermal system solutions for the electronics and photovoltaic industries, and is recognized as a leader in technology and innovation for the modern and cost-effective manufacturing of electronic assemblies. As a global manufacturer, we offer a wide range of products, including convection, condensation, or vacuum reflow soldering systems, drying and coating equipment, functional testing systems, equipment for the metallization of solar cells, and numerous custom solutions. With over 30 years of industry experience, we operate in all significant growth markets and provide innovative manufacturing solutions that set industry standards.